ギア設計の実践 | 初心者のための機械設計入門
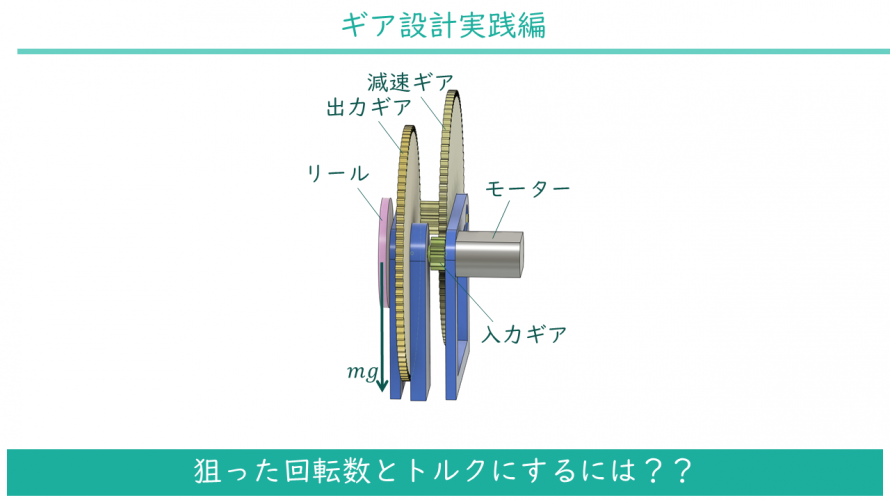
前回学んだことをもとに、より具体的にギア設計をして見ましょう。
ミニ四駆などで使用されているサイズのDCモーターを減速して、200gのモノを持ち上げられるようにしてみましょう。
構成の概略は下図の通りで、モーターの回転をギアで減速し、半径20mmのリールで紐を巻き取ります。
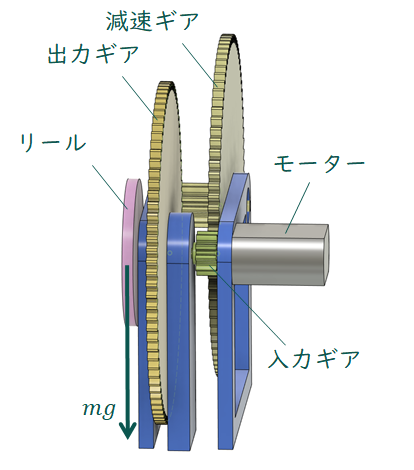
モーター特性
今回は秋月電子通商で簡単に手に入るこちらのDCモーターを使用することにします。
ギア設計をするために、まずはモーターの特性を理解する必要があります。一般的にモーターのメーカーが次のようなデータシートを公開しています。
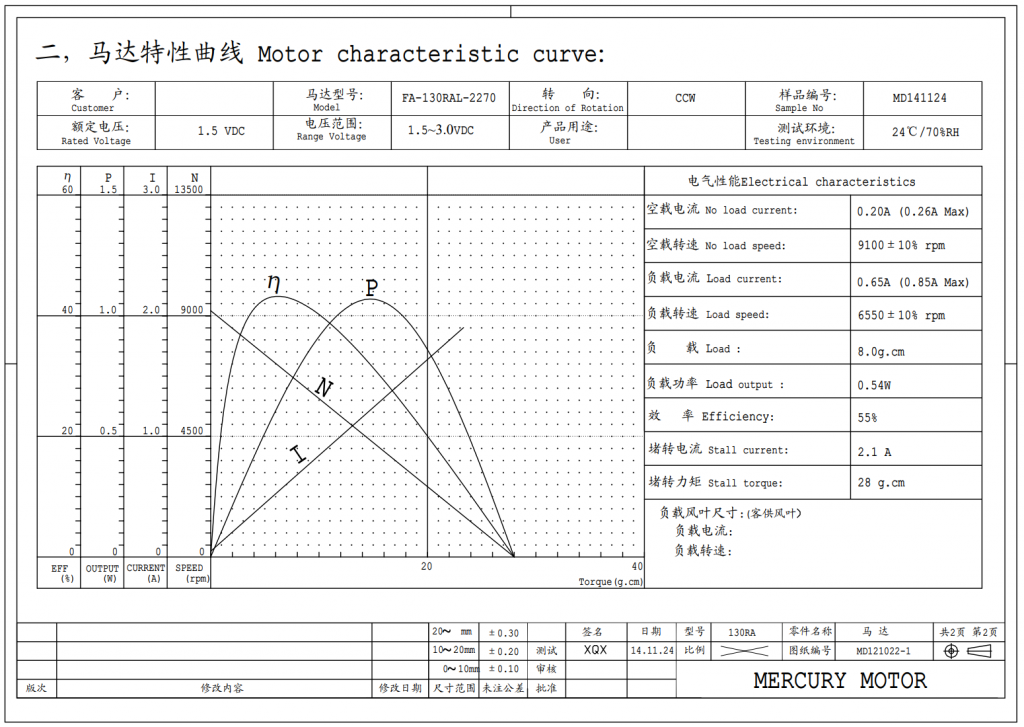
グラフの横軸は負荷トルクになっており、負荷に応じてI,N,P,ηが変化することがわかります。
このグラフでは、Iは電流(Current)、Nは回転数(Speed)、Pは出力(Output)、ηは効率(Efficiency)を表しています。
出力Pというのは仕事率で、一秒間に供給できる機械エネルギーを表します。
効率というのは入力した電気エネルギーからどれだけの機械エネルギーを出力できるかを示しています。
エネルギーについての詳細はこちらをご参照ください。
今回は効率が最も良い6gcm付近でモーターを回すことにします。このときの回転数は約5500rpmです。
これまでトルクの単位は[Nm]として説明してきましたが、実は力×長さの組み合わせであればなんでもOKです。今回出てきたgcmもトルクの単位で、gf×cmということを表しています。gは質量の単位である一方、gfは力の単位なので、gcmという表記は本来不正確です。しかしgfcmと同じ意味でgcmという表現もよく使用されています。
gf(グラム重)は時間の単位で、1gの物体を手で持った時に、手に加わっている力を1gfと定義しています。つまり単位[N]の力で言うと、\(mg=0.001 \mathrm{ kg}\times9.81 \mathrm{ m/s^2}=0.00981N\)が1gfと等しくなります。
学校では[N]しか使いませんが、実務ではほぼすべて[gf]を使って話が進むので両方使いこなせるひつようがあります。今回は練習がてら[gf]を使って説明を続けます。わからないところはコメントください。
ギア設計
ギア設計はExcelやスプレッドシートなどの表計算ソフトを用いて行うのが効率的です。今回はExcelを使って計算します。
出力トルクと減速比
半径20mmの所に200gfの負荷がかかるので、リールに働くトルクは\(200\mathrm{gf}\times20 \mathrm{mm}=4000 \mathrm{ gfmm}=400 \mathrm{ gfcm}\)となります。
モータートルクは6gfcmなので減速比は\(400/6=67\)程度になるはずです。
したがって出力回転数は\(5500/67=82 \mathrm{ rpm}\)程度になるはずです。
ここまでで入出力の値がわかったのでシートに記入しておきます。今回は出力トルクが重要なので、出力回転数はぴったりになる必要はありません。このような値を参考値と言います。

1段減速の場合
まずは、モーターに結合された入力ギアと、リールに結合された出力ギアの2つのギアだけで構成される1段減速の場合を考えてみます。
早速、モジュールと歯数を決めていきましょう。
200gのものを持ち上げる程度の負荷であれば、モジュールは0.5程度でも十分な強度になりそうですが、3Dプリンタで造形するため造形のし易さからモジュールは大きめの1とします。B列に入力します。
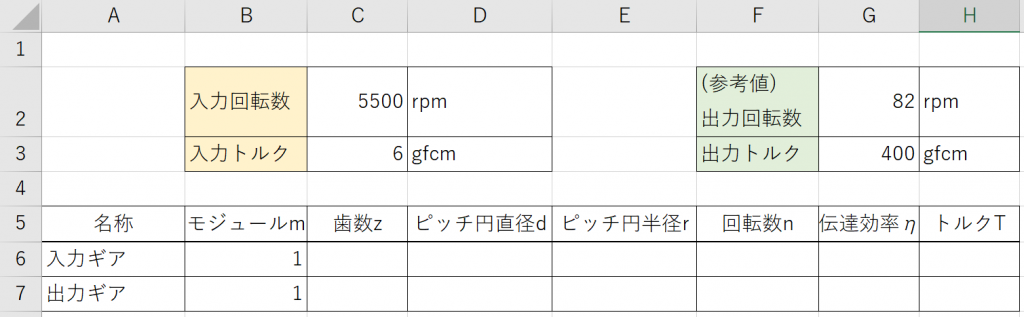
入力ギアの歯数を10、出力ギアをの歯数を100と仮に設定します。この値は後で調整します。C列に入力します。
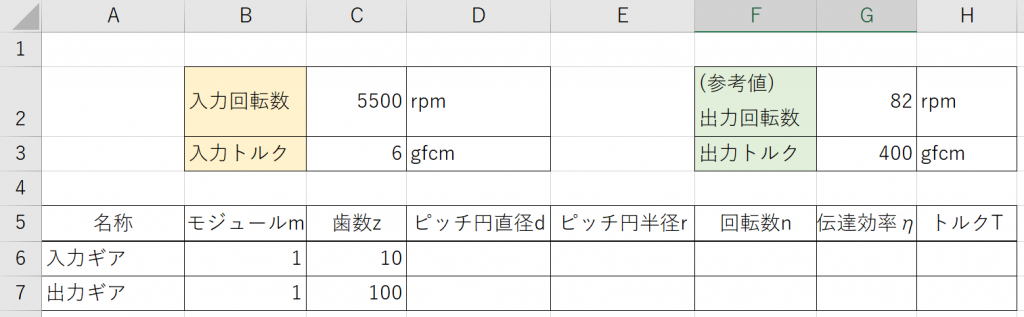
復習になりますが、ピッチ円直径dは\(mz\)で求めることができました。ついでに2で割った半径も計算しておきます。D列、E列に入力しておきましょう。
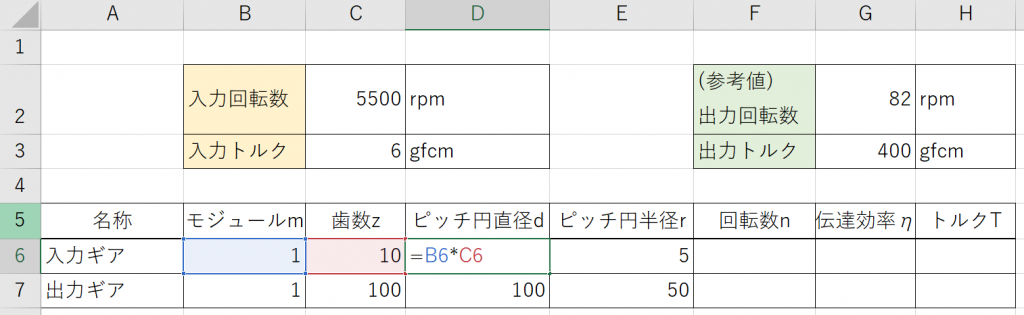
歯数が決まっているので各ギアの回転数を求めることができます。入力ギアの回転数はモーターと一致するのでセルC2の値を参照します。
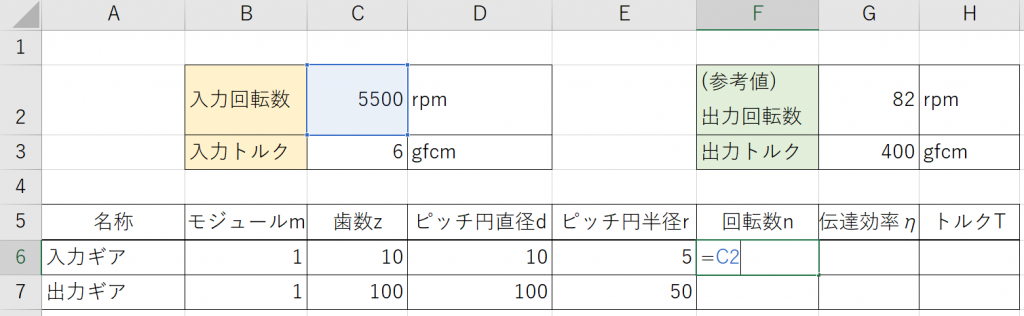
出力ギアの回転数は列に入力した歯数を使って\(\frac{z_1}{z_2}n_1\)で求めることができます。セルF7に入力しておきます。
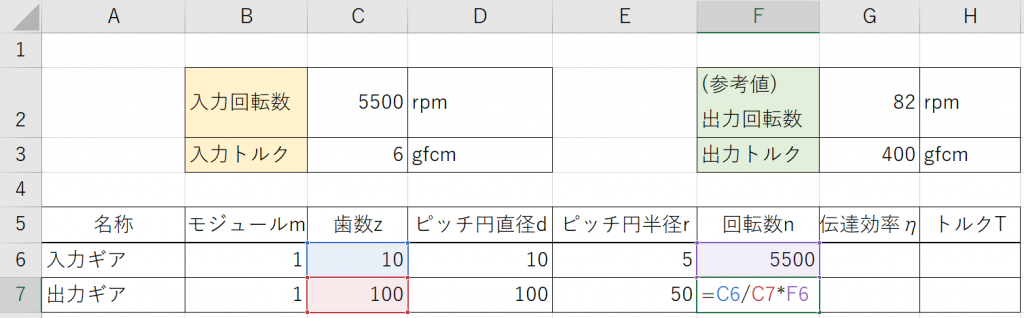
トルクも同様に、入力側はモーターと一致するので、セルC3を参照します。
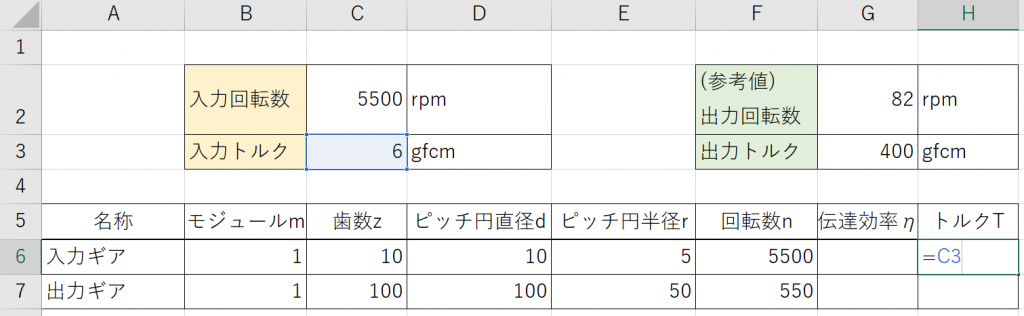
出力ギアのトルクは\(\frac{z_2}{z_1}T_1\)で求めることができます。セルH7に入力しておきます。
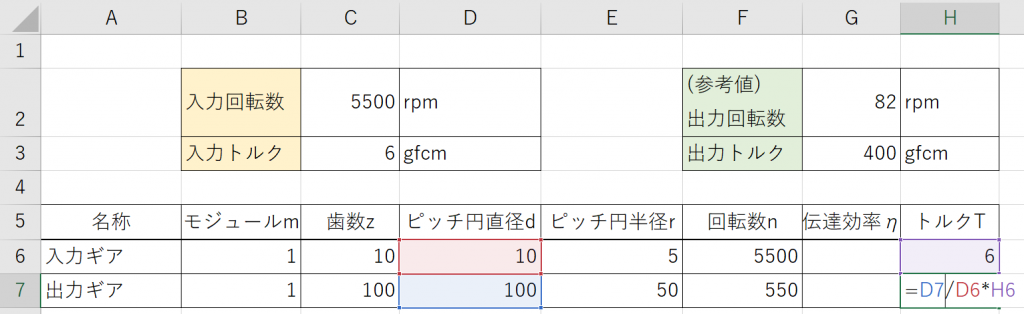
ただトルクはもう少しだけ考慮すべきことがあります。
ギアは自身も回転運動をしているため、摩擦などによるエネルギー損失があります。そのため入ってきたエネルギー(≒トルク)のすべてを次のギアに伝えるということはできません。次のギアへ伝えることができるエネルギーの割合を伝達効率と言います。
今回は伝達効率\(\eta\)(イータ)を90%とします。
先程求めたトルクに伝達効率も掛けます。
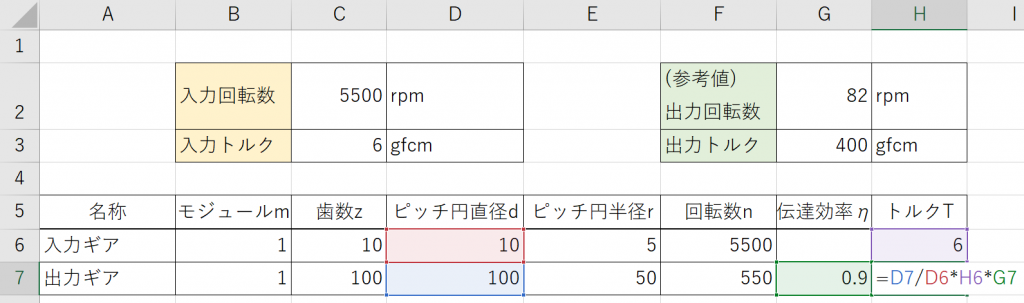
一通りの入力が終わりましたが、現段階では出力トルクは54gfcmになっており、目標に達していません。これはギアの歯数を適当に決めているためです。歯数を調整しましょう。
入力ギアの歯数は10と言うことにして、出力側の歯数を変えてみましょう。いろいろ試してみると、歯数が741のときに目標としている出力トルクを超えることがわかります。(ソルバー使える方はソルバーで解いてください)
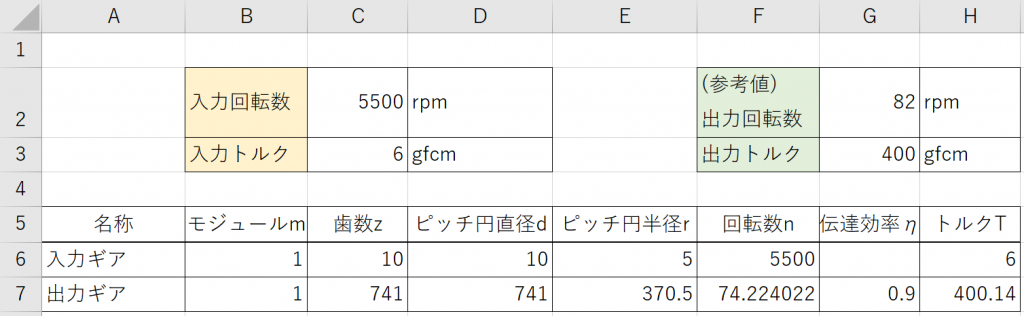
これでギア設計はひとまず完了です。
しかし、この設計には問題があります。それは出力ギアが大きすぎるということです。小型のモーターで直径40mmのリールを回したいだけなのに、ギアの径が約740mmというのはバランスが悪すぎます。
あえて軸間距離を大きくしたい場合などはこの設計で良いですが、一般的にはもう少し小型にしたくなります。
この問題を解決するためにギアを二段目、三段と増やしていきます。二段が理解できれば三段以降は同じなので今回は二段の設計をしてみます。
2段減速の場合
入力ギアと出力ギアの間に減速ギアを追加します。減速ギアは段付きギアになっています。モジュールはそろえる必要があるので1にし、歯数は仮に100と10にしておきます。ピッチ円の式は先ほどと同じです。
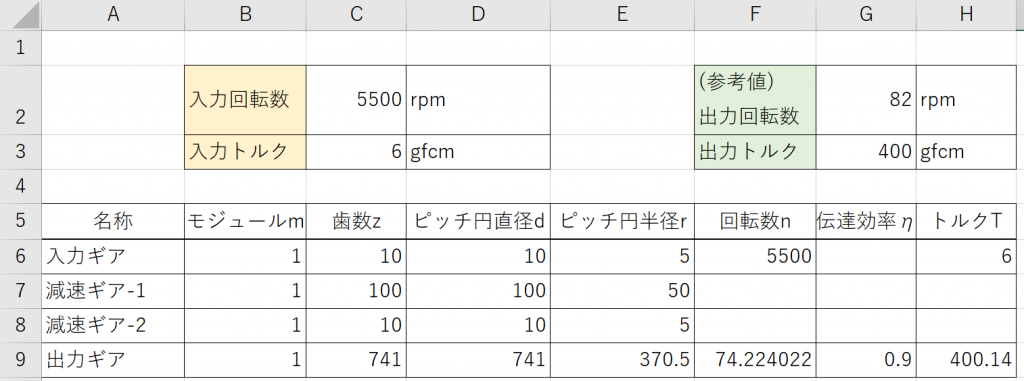
まずは回転数を計算します。減速ギア-1の回転数は1段減速の時の出力ギアと同じ考え方になります。
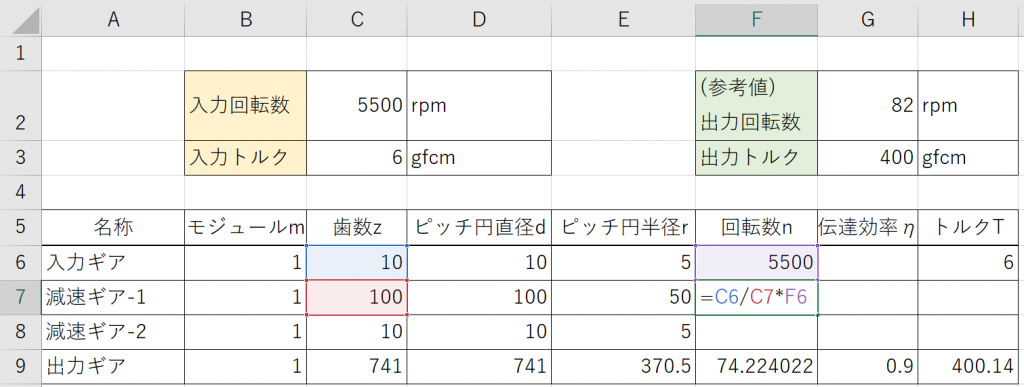
段付きギアなので、減速ギア-2と減速ギア-1は一体となっており、同じ回転数になります。
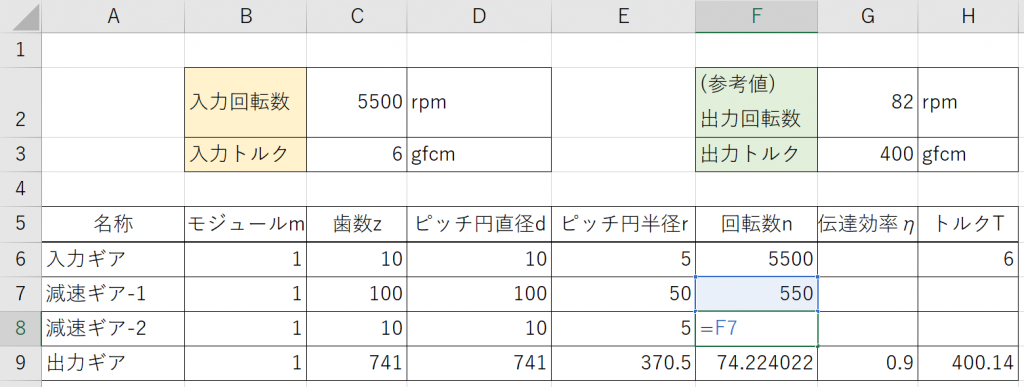
出力ギアの回転数も修正します。
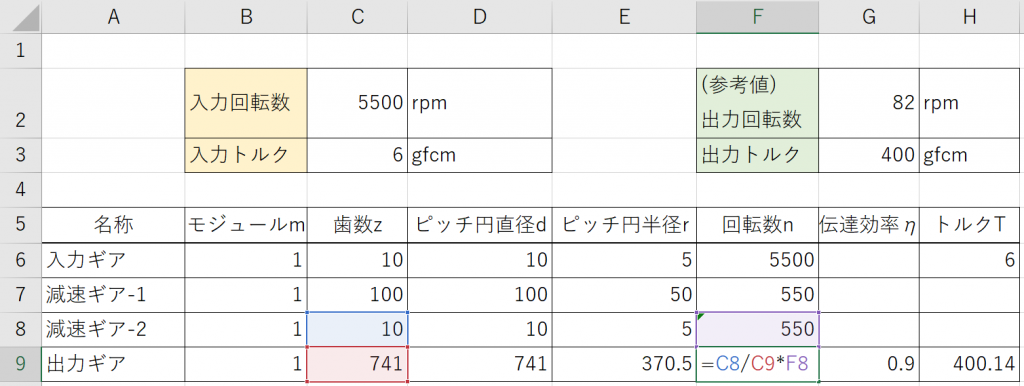
続いてトルクです。減速ギア-1は次のようになります。
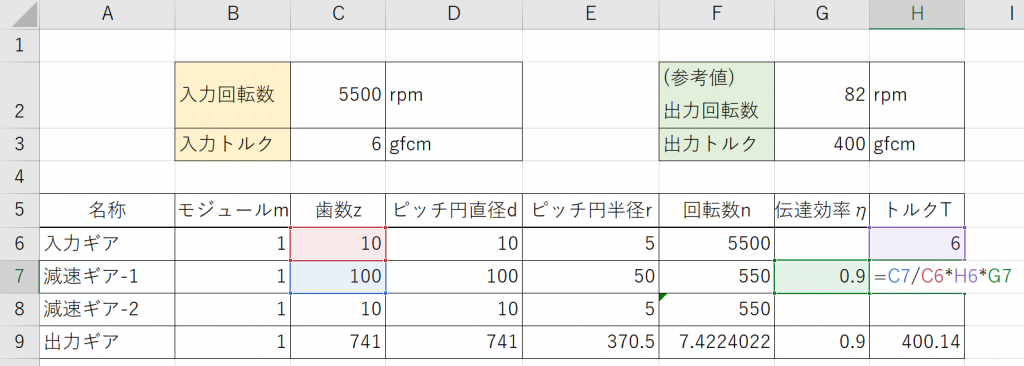
段付きギアで一体となっているので、減速ギア-1と減速ギア-2はトルクも一致します。
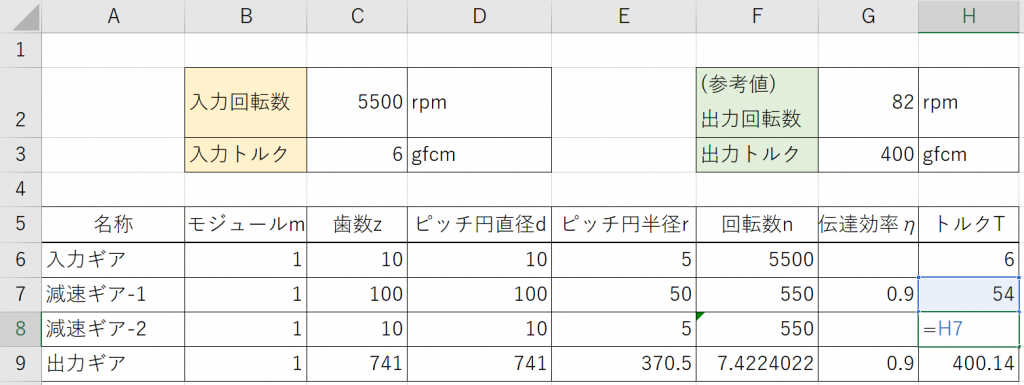
出力ギアは次のようになります。
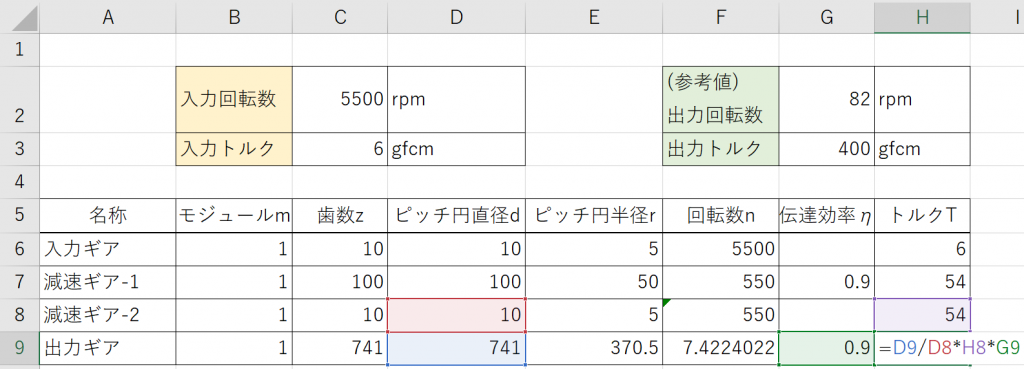
これで入力が一通り終わりました。出力ギアの歯数を修正していないので今度は減速が大きくなりすぎています。全体的に歯数を調整しましょう。
出力ギアのトルクが目標値である400gfを超えていればどんな組み合わせでもひとまずOKです。私はこんな感じにしてみました。
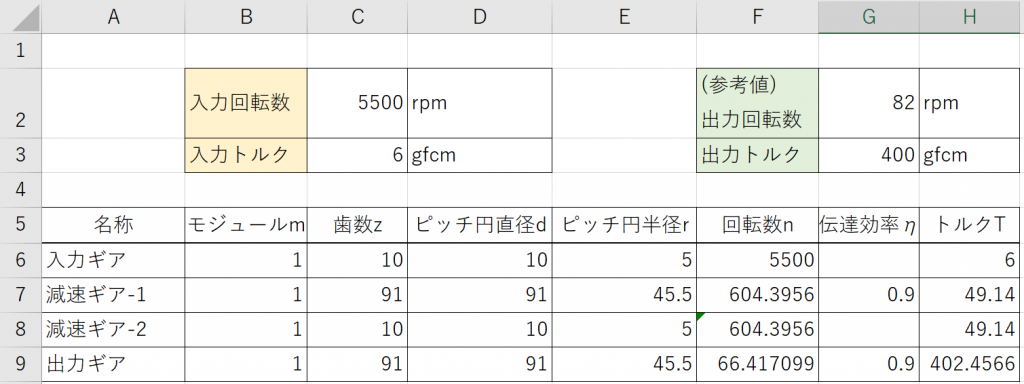
今度は一番大きいギアでも直径約91mmで収まるようになりました。先ほどの740mmとは雲泥の差で、かなり小型化できたと思います。
このサイズでも満足できなければ3段減速機にすることでより小型化ができます。
しかし、噛み合うギアが多くなればなるほど、伝達効率を掛けなければならない部分が増えるため、全体としても効率が落ちていくということに注意してください。段数を増やせばよいというものでもありません。
また、噛み合うギアの歯数の最小公倍数が極力大きくなるようにするというのもポイントです。
今回は10歯と91歯で噛み合うようにしました。 10歯と91歯の最小公倍数は910になるので、910歯進むと両方のギアの位置が元通りになります。言い換えると、91歯のギアが10周してやっと元通りになります。この場合、91歯のギアの歯は10周に1回同じ歯と噛み合うことになります。
しかし、もしこれが10歯と90歯だとすると、最小公倍数が90となり90歯進んだだけで元通りになってしまいます。この場合、90歯のギアが1周するごとに元通りになるということなので、90歯のギアの歯が噛み合う相手の歯は常に同じ歯になってしまいます。
同じ歯と繰り返し係合するのは摩耗などの観点から避けるべきです。
もっともよいのはかみ合うギアの歯数が「互いに素」になっていることです。
この設計をもとに簡単に3Dモデルを作成すると次のようになります。
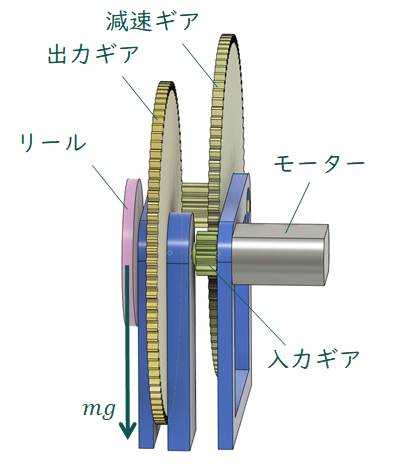
リールとモーターのサイズ感と照らし合わせると、ギアはまだ大きいような気もしますが、これで許容されるケースも多いと思います。
まとめ
エクセルを使って2段ギアの設計をできるようにしました。
本当は今回説明した回転数・トルクの設計以外にも、強度計算や、摺動部の摩耗の計算なども行って問題ないことを確認する必要があります。
しかし、耐久性を無視すればこのまでの設計でそこそこ動くものが作れると思います。
趣味レベルであれば、回転数とトルクだけ合わせてプロトタイピングし、問題が発生したら都度対処すればよいと思います。
-
前の記事
ギア設計の基礎知識 | 初心者の為の機械設計 2021.06.13
-
次の記事
記事がありません